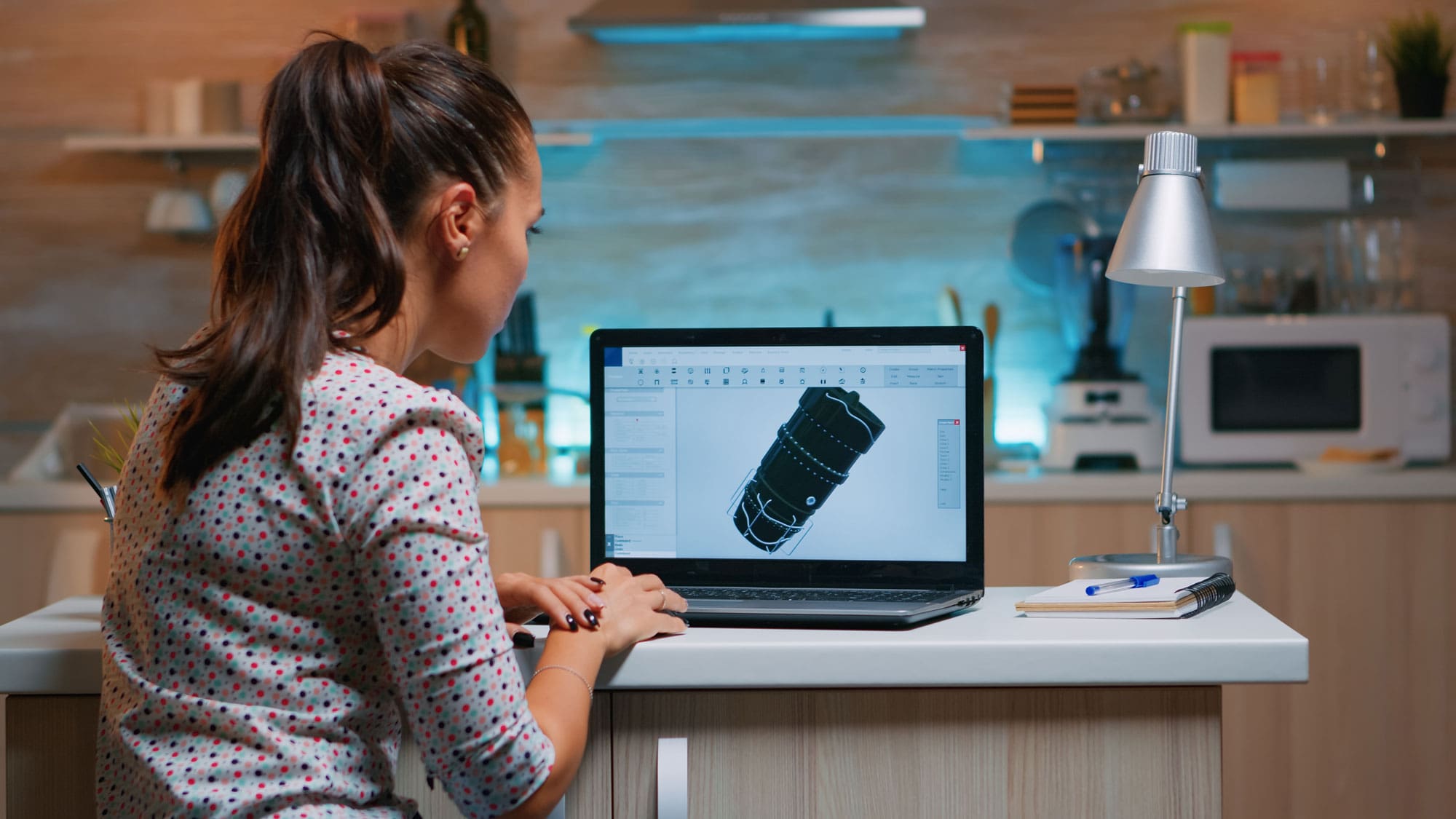
Computer Numerical Control (CNC) machining has revolutionized the manufacturing industry over the years, allowing for precise and efficient production of complex parts. Since its inception in the mid-20th century, CNC machining has undergone significant advancements, pushing the boundaries of what is possible in terms of accuracy, speed, and versatility. In this article, we will explore the evolution of CNC machining and delve into its projected future, where groundbreaking technologies promise to reshape the manufacturing landscape.
The Early Days: Birth of CNC Machining
The concept of CNC machining emerged in the late 1940s and early 1950s when engineers sought ways to automate the machining process for increased productivity and accuracy. In 1952, the Massachusetts Institute of Technology (MIT) introduced the first CNC milling machine, which was programmed using punch cards. This marked the beginning of a new era in manufacturing, where manual operations were replaced by automated processes.
The Rise of CAD/CAM and CNC Integration
During the 1960s and 1970s, Computer-Aided Design (CAD) and Computer-Aided Manufacturing (CAM) systems gained prominence, allowing engineers to create and optimize digital models of parts. These models could then be translated into instructions for CNC machines, eliminating the need for physical templates or manual programming. This integration of CAD/CAM systems with CNC machines brought about a significant leap in productivity and flexibility, as manufacturers could quickly iterate designs and produce complex components with greater ease.
Advancements in Control Systems and Precision
The 1980s and 1990s witnessed notable advancements in CNC machining. The control systems became more sophisticated, with the introduction of microprocessors and servo motors. This allowed for higher precision, faster spindle speeds, and smoother movements of the cutting tools. The integration of sensors and feedback mechanisms further enhanced accuracy, enabling the machines to adjust for any deviations during the machining process.
Multiaxis Machining and Complex Geometries
As the demand for intricate parts increased, multiaxis machining capabilities were developed. Traditional three-axis machines were expanded to include fourth and fifth axes, enabling the machining of complex geometries and curved surfaces. With the ability to tilt, rotate, and reposition the workpiece, manufacturers could produce parts with intricate details that were previously unattainable. This advancement opened up new possibilities across various industries, such as aerospace, automotive, and medical.
Automation and Robotics in CNC Machining
In recent years, automation and robotics have played a significant role in transforming CNC machining. Robotic arms equipped with advanced end effectors can handle multiple tasks simultaneously, such as loading and unloading workpieces, tool changes, and quality inspection. Collaborative robots, or cobots, have also emerged, working alongside human operators to enhance productivity and safety in the manufacturing environment. These advancements in automation have not only increased production efficiency but also reduced labor-intensive tasks, allowing human workers to focus on higher-level responsibilities.
The Future of CNC Machining: Integration of AI and Additive Manufacturing
Looking ahead, CNC machining is poised to undergo further evolution driven by two key trends: the integration of artificial intelligence (AI) and the convergence of CNC with additive manufacturing, also known as 3D printing.
AI holds immense potential in optimizing machining processes. By leveraging machine learning algorithms and real-time data analysis, AI can optimize tool paths, predict tool wear, detect anomalies, and fine-tune machining parameters for optimal results. This will lead to reduced cycle times, improved accuracy, and increased efficiency.
The convergence of CNC machining with additive manufacturing will bring together the best of both worlds. CNC machines will be capable of not only subtractive manufacturing but also incorporating additive processes, enabling the creation of hybrid components with complex internal structures and improved material properties. This integration will unlock new design possibilities and accelerate the production of functional prototypes, customized parts, and small production runs.
CNC machining has come a long way since its inception, revolutionizing the manufacturing industry and empowering engineers to create intricate and precise parts. From early punch card systems to sophisticated CAD/CAM integration, and from multiaxis machining to automation and robotics, CNC machining has continuously pushed the boundaries of what is achievable. The future of CNC machining looks promising, with AI-driven optimization and the integration of additive manufacturing poised to redefine precision, speed, and design possibilities. As these technologies continue to advance, CNC machining will play a crucial role in shaping the future of manufacturing.